پس پردازش سیستم نمونه
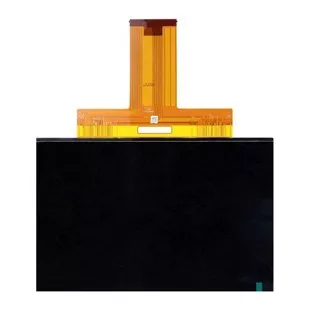
بیشتر فرایند های تولید افزایشی برای آماده سازی قطعه پس از ساخت برای فرم ،تنظیم و یا کاربرد نهایی ، نیاز به پس پردازش دارند. براساس تکنیکی از AM بر روی تکنیک هایی از پس پردازش تمرکز خواهد کرد که برای ارتقاء عناصر یا غلبه بر محدودیت های AM استفاده می شوند.
این تکنیک ها شامل موارد زر می باشند:
1. حذف مواد ساپورت ها
2. بهبود بافت سطح
3. بهبود ظرافت ها
4. بهبود زیبایی شناختی ها
5. آماده سازی برای استفاده به نوان یک الگو
6. ارتقاء ویژگی ها با استفاده از نکنیک غیر گرمایی
7. ارتقاء ویژگی ها با استفاده از تکنیک های گرمایی
مهارت کاربران مختلف تکنولوژی تولید افزایشی در انجام پس پردازش، یکی از بارزترین ویژگی آنها در میان رقابت ارائه دهندگان خدمات می باشد. شرکت هایی که می توانند به شکلی مفید و دقیق کار پس پردازش قطعات را مطابق با انتظارات مشتری انجام دهند معمولا به خاطر خدماتشان پاداشی هم دریافت می کنند؛ در حالیکه، شرکت هایی که در ابتدا بر روی قیمت رقابت می کنند ممکن است کیفیت پس پردازش را فدای کاهش هزینه ها نمایند. همچنین برای دیدن دستههای رزین uv میتوانید به لینک مربوطه مراجعه نمایید.
حذف مواد و ساپورت ها
حذف ساپورت ها، یکی از رایج ترین ها در پس پردازش تکنولوژی تولید افزایشی است. موادی که در ساپورت ها استفاده می شوند را می توان به صورت گسترده به دو بخش طبقه بندی کرد:
( الف) موادی که به صورت طبیعی به عنوان محصول فرعی فرایند ساخت، قطعه را در برمی گیرند( ساپورت های طبیعی ) و ( ب) ساختارهای محکمی که برای سایت، نگهداری یا اتصال قطعه در حال ساخت به سطح ساخت، طراحی و ساخته می شوند( ساپورت های مصنوعی ).
پس پردازش ساپورت های طبیعی
در فرایندهایی که مواد ساخت قطعه، آن را کاملا در طول فرایند دربرمی گیرند،باید قبل از استفاده از قطعه، آن را کاملا از مواد اطرافش جدا کرد. فرایندهایی که ساپورت های طبیعی را فراهم می کنند اصولا فرایندهای پودری و صفحه ای هستند.بخصوص، تمامی فرایندهای ذوب بستر پودر (PBF) و پاشش همبند به جداسازی قطعه از پودرهای بلا استفاده ای که اطراف آنرا فرا گرفته اند، احتیاج دارند؛ و فرایندهای لمینت سازی فلزی صفح اتصال – سپس – شکل نیز به برداشتن مواد صفحه ای پوشانده شده، نیازمند است.
در فرایندهای PBF پلیمری، بعد از اینکه قطعه ساخته شد، وارد کردن آن به مرحله خنک سازی الزامی است. قطعه باید در همان حالت، درون پودرها باقی بماند تا از ایجاد انحراف در آن، در طول خنک سازی غیریکنواخت جلوگیری شود. زمان خنک سازی به مواد ساخت و اندازه قطعه (قطعات ) بستگی دارند. وقتی کار خنک سازی انجام شد، شیوه های مختلفی برای جداسازی قطعه ( قطعات ) از پودرهای بلا استفاده اطرافشان وجود دارد. معمولا، کل ساخت ( قطعه ساخته شده از پودرهای بلااستفاده و بخش های ذوب شده ) به صورت یک توده از درون دستگاه برداشته و به بخش « قالب شکنی » منتقل می گردد که در آنجا قطعات به صورت دستی از مواد پودری اطرافشان جدا می شوند در حالیکه ابزار کار با چوب و ابزار تمیز کردن دندانپزشکی معمولا برای برداشتن پودرهایی به کار برده می شوند که بر روی سطح رسوب شده اند یا آن هایی که درون کانال ها یا ترکیبات کوچک گیر کرده اند. حفره های داخلی و فضاهای خالی به سختی قابل تمیز کردن هستند و ممکن است به زمان قابل توجهی برای پس پردازش نیاز داشته باشند.
به استثنای زمان خنک سازی طولانی، تکنیک های حذف ساپورت های طبیعی در فرایندهای پاشش همبند برای آنهایی که در PBF مورد اتفاده قرار می گیرند بسیار الزامی هستند. در بیشتر موارد، قطعاتی که با استفاده از پاشش همبند ساخته می شوند، در زمان خروج از دستگاه بسیار شکننده می باشند. از این رو، تا زمانیکه قطعه با شیوه نفوذ تقویت نشده است، قطعات باید با دقت جا به جا شوند. این مسئله در مورد مواد PBF که به نفوذمواد پس از ساخت احتیاج دارند هم صدق می کند مانند بعضی از مواد الاستومری، مواد پلی استرین برای ریخته گری و قطعات سبزفلزی و سرامیکی.
اخیرا، فرایندهای مکانیزه برداشتن پودرهای بلااستفاده نیز توسعه پیدا کرده اند. این کارها می توانند به صورت دستگاه های مجزا یا در ترکیب با مخزن ساخت انجام شوند. یکی از اولین دستگاه های پاشش مواد همبند ZCorp ( که اکنون 3D Systems نامیده می شود). چندین تولید کننده دستگاه PBF فلزی نیز شروع به ترکیب تکنیک های نیمه مکانیزه برداشتن پودرها در دستگاه هایشان کردند. روند های اخیرا نشان می دهد که بسیاری از ماشین های PBF و پاشش همبند، همزمان با تکمیل قطعه، حذف مکانیزه پودر را هم انجام خواهند داد.
فرایندهای لمینت سازی صفحه ای اتصال –سپس- شکل، مانند دستگاه Mcor، نیز به برداشتن مواد ساپورت های طبیعی قبل از استفاده از قطعه نیاز دارند. اگر هندسه های پیچیده ای با زوایای بیرون زده، حفره ها یاکانال های داخلی و مختصات خوب به کار روند، ممکن است برداشتن ساپورت ها خسته کننده و زمان بر باشد. اگر حفره ها یا کانال های محصوری ایجاد شود، لایه لایه کردن مدل در ارتفاع مشخص z برای دستیابی به مکعب زدایی بخش های داخلی الزامی است و سپس بعد از برداشتن مواد اضافی ساپورت ها، دوباره چسبانده می شود.
حذف ساپورت های مصنوعی
فرایندهایی که به صورت طبیعی ساپورت نمی کنند برای زوایای بیرون زده به ساپورت استراکچرهای مصنوعی احتیاج دارند. در بعضی موارد، مانند در زمان استفاده از تکنیک های PBF برای فلزات، ساپورت های مصنوعی نیز برای مقاومت در برابر انحراف قطعه مورد نیاز هستند. ساپورت های مصنوعی، می توانند از همان مواد تولید قطعه یا از مواد ثانویه ساخته شوند. توسعه مواد ثانویه ساپورت ها، یک مرحله اصلی در ساده سازی حذف ساپورت های مصنوعی می باشد زیرا این مواد به صورتی طراحی می شوند که ضعیف تر از مواد ساخت، حلال در محلول های یا قابل ذوب در دمایی پایین تر از مواد ساخت باشند.جهتگیری قطعه در رابطه با محور ساخت اولیه مشخصا بر تولید و حذف ساپورت تاثیر می گذارد.
سخن تکمیلی
اگر برای مثال، یک قطعه باریک به صورت خوابیده و مسطح باشد، میزان مواد ساپورت هایی که مصرف می شود ممکن است از میزان مواد برای ساخت بیشتر باشد.جهتگیری ساپورت ها نیز بر پرداخت سطح قطعه تاثیر دارد، زیرا برداشتن آنها معمولا « نشانه شاهد» برامدگی یا شیاری را در جایی که ساپورت – ها متصل شده اند به جا می گذارد، علاوه بر این، استفاده ازساپورت ها در نواحی با مختصات کوچک ممکن است در زمان برداشتن ساپورت ها موجب شکستن این نواحی شود. از این رو، جهت گیری و موقعیت ساپورت ها عامل اصلی بیشتر فرایندها برای رسیدن به ویژگی های مطلوبی از قطعه پرداخت شده، می باشد. از طرین لینک مربوطه میتوانید به دستهبندی فیلامنت دسترسی یابید.
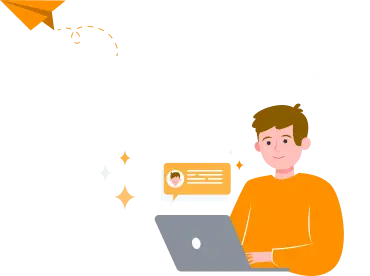