موضوعات مربوط به بررسی مواد
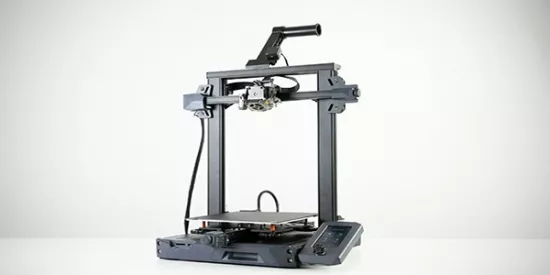
مواد تکنولوژی تولید افزایشی علاوه بر مبحث ماشین آلات معمولا به بررسی های دقیقی نیازمندند. مواد خام استفاده شده در فرایندهای AM دارای طول عمر محدودی هستند وباید در شرایطی نگه داشته شوند که مانع واکنش و فرسایش شیمیایی در آنها گردد . از قرار گیری در معرض رطوبت و نور زیاد باید خودداری شود. بیشتر فرایندها از موادی استفاده می کنند که برای مصرف بیش از یک بار قابل استفاده می باشند. به هرحال ، ممکن است اگر مواد چندین بار استفاده شوند ، کیفیت شان کاهش پیدا کند و در نتیجه شیوه ای برای حفظ ثبات در کیفیفت مواد در طول چرخه بازیافت باید در نظر گرفته شود.
بررسی مواد
با اینکه مواد ایمن متعددی برای قرار گیری در معرض رزین های پلیمری نور پز بصورت طولانی وجود دارد اما اکثرمواد خام پلیمرهای AM برای کار ایمنی دارند. مواد پودری باید در کل از نظر دارویی بی اثر باشند، اما وجود میزان زیادی از آنها در محیط کار می تواند آنجا را لغزنده نمونده، مکانیزم را آلوده کرده و مشکلات تنفسی ایجاد کند. علاوه بر این، پودر های واکنشی، احتمال وقوع آتش سوزی دارند. این موارد ممکن است در صورتیکه دستگاه به جای قرار گیری در یک کارگاه، در یک محیط مرکزی طراحی استفاده شود، مشکلاتی را ایجاد نماید. فروشندگان سیستم AM تلاش زیادی را صرف ساده سازی کار با مواد کردند بارگذاری مواد جدید معمولا فرایندی است که به صورت آفلاین یا با حداقل تغییرات در طول زمان قابل انجام است در نتیجه دستگاه ها می توانند به صورت مداوم در حال کارباشند. سیستم های نرم افزاری معمولا به شکلی با مواد تنظیم شده اند که می توانند مواد مختلف را شناسایی نموده و شاخص های ساخت را با آنها تطبیق دهند. برای دیدن محصولات پرینتر سه بعدی به لینک مشخص شده مراجعه نمایید.
بسیاری از مواد با دقت بسیار بالا جهت کار با یک تکنولوژی خاص AM تنظیم شده اند. در مورد استفاده مواد دسته سوم، معمولا گارانتی هایی وجود دارد که کاربر باید از آنها اطلاع داشته باشد. از آنجا که بعضی از پودرهای رسوب شده لیزر پلیمری، برای مدت طولانی در دمای بسیار بالا نگهداری می شوند، ممکن است افزودنی هایی داشته باشند که از اکسیده شدن و کاهش کیفیت آنها جلوگیری کند. همچنین، مواد اکسترودر شده به مقاومت ابعادی بسیار شدیدی احتیاج دارند که معمولا در تجهیزات اکسترود کننده عادی وجود ندارد. از آنجا که نیروی پیشران مواد اکستروژی در طول دستگاه به رشته های خروجی فشار وارد می کند، تغییرات در ابعاد آنها ممکن است باعث لغزش گردد. به علاوه، شاخص های ساخت بر طبق مواد استاندارد استفاده شده، طراحی می گردند. از آنجایی که روش های فرمولاسیون مواد بسیار متنوع است، جابه جایی یک ماده به جای دیگری، حتی اگر ظاهرشان مشابه باشد، ممکن است ستاپ قطعات و بهبود شاخص های فرایند به دقت بالایی احتیاج داشته باشد.
بعضی از ماشین ها این امکان را به کاربر می دهند تا تمام یا بخشی از مواد مورد استفاده در یک دستگاه را بازیافت نمایند اما این موضوع برای مواد مصرفی که در ساخت قطعه قبلی به کار رفته، صادق نیست. این شرایط بخصوص در مورد سیستم های پودری کاملا صدق می کند. هم چنین رزین های پلیمری نورپز هم قابل استفاده مجدد هستند. به هرحال، مصنوعات و دیگر آلاینده - هایی در موارد بازیافت شده وجود دارد که بررسی، انتخاب یا صاف کردن مواد قبل از بازگرداندن آنها به دستگاه را بسیار ضروری می سازد. برای مثال بسیاری از مواد رسوبی لیزری که از ساخت قبلی به جا مانده اند، به دلیل باقی ماندن موهای فرچه پاک کننده، کاملا از بین رفته اند.
طراحی
طراحان و کاربران باید در زمان ستاپ دستگاه تولید افزایشی به چندین عامل توجه داشته باشند.
جهت گیری قطعه
اگر در نهایت یک سیلندر ساخته شود، این قطعه باید ساخته شده از مجموعه ای از لایه ها باشد که هرکدام از آنها بر روی دیگری می باشد. حتی اگر لبه های لایه ها در تمام فرایندهای AM کاملا عمودی نباشند، نتیجه آن معمولا یک سیلندر خوب با لبه نسبتا صاف خواهد بود. سیلندر مشابهی نیز ممکن است ساخته شود که در کناره های آن الگوهای لایه های پلکانی به وضوح قابل رویت باشند. این کار منجر به تولید مجدد اطلاعات CAD با دقت کمی می شود که از نظر زیبایی بسیار کیفیت پایینی دارد. علاوه بر این، به دلیل اینکه فرایند لایه سازی در بیشتر دستگاه های AM زمان زیادی را می برد، ساخت یک سیلندر بلند به صورت عمودی خیلی بیشتر از یک سیلندر افقی زمان خواهد برد. به هرحال در مورد فرایند های اکستروژن مواد، زمان ساخت یک قطعه به تنهایی، عاملی است که مربوط به کل حجم ساخته شده (شامل ساپورت ها ) می باشد و در نتیجه یک سیلندر باید همیشه در صورت امکان عمودی ساخته شود.
آنچه که بر دقت قطعه اثر می گذارد جهت گیری آن در یک دستگاه می باشد. از آنجایی که بسیاری از قطعات در طول چند محور دارای خصوصیات پیچیده ای خواهند بود، نمی تواند جهت - گیری مطلوبی برای یک قطعه خاص باشد. علاوه بر این، حفظ هندسه بعضی از مختصات در مقایسه با دیگر مشخصات می تواند خیلی مهم باشد.در نتیجه جهت گیری درست ممکن است مرجع قضاوت باشد. این قضاوت ممکن است متناقض با موارد دیگر مانند زمان ساخت قطعه باشد ( مثلا قطعات ساخته شده ی بلند تر، زمان بیشتری نسبت به قطعات کوتاه تر می برند در نتیجه قطعات با وجوه بلند تر بهتر است خوابیده ساخته شوند )، رویکرد وجهی مشخص می تواند نیاز به ساپورت های بیشتری را طلب کند. سطوح خاص هم برای اینکه صافی سطح نهایی مناسبی را عرضه کنند، می توانند به صورت رو به بالا ساخته شوند در این صورت با ساپورت استراکچر ها هم تداخلی پیدا نمی کنند.
سخن تکمیلی
به طور کلی در تکنولوژی تولید افزایشی، وجوه رو به بالا از کیفیت مطلوب تری برخوردار هستند. دلیلش بستگی به نوع فرایند دارد. برای مثال، در بسیاری از فرایند ها وجوه رو به بالا با ساپورت های مورد نیاز در تماس نیستند. برای بستر های پودری، قطعات رو به بالا صاف تر می شوند زیرا در مقابل هوا منسجم گشته و در نتیجه دارای بافتی پودری شکل می شوند. در مورد فرایندهای اکستروژن، سطوح رو به بالا با نوک اکستروژن صاف شده اند. از این رو، قانون کیفیت قطعات رو به بالا، یکی از چندین قانون کلی است که معمولا برای تمامی فرایند های AM کاربرد دارند. برای دیدن محصولات اسکنر سه بعدی به لینک مشخص شده مراجعه نمایید.
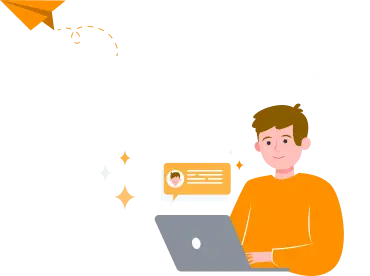